
Automatic Balancing Damper Manual Or Automatic
Automatic Round Damper (ARD) APPLICATION The ARD is a round damper with a 24 Vac, spring-return damper motor used to control circulating air in heating, cooling, and ventilating systems. The damper is shipped as a powered closed/spring return open damper. The damper can be field-converted to a power open/spring return closed damper when used as anIts operation can be manual or automatic. Manual dampers are turned by a handle on the outside of a duct.
Increasing the electric power input leads to higher superheating of the refrigerant and so the proportion of heat released at high temperature level (Q CH2) is increased. By varying the electrical power input the compressor unit offers some flexibility in operation. After the enthalpy increase due to the compression the refrigerant releases heat at a higher temperature (Q CH2) in a desuperheater and at a lower temperature in a condenser (Q CH1). ABD automatic balancing damper adjusts exhaust airflow rates based on pressure readings from integral test and balance ports in Capture Jet exhaust hoods.The chiller that provides cooling services performs similar to a heatpump. This damper does not come with blade or side seals as it is designed for applications that restrict the amount of air flow down a duct. The BD-1600 Balancing / Zone damper is designed for manual balancing or automated zone control applications in air flowing heating, ventilating and air conditioning systems.
In between, there is linear interpolation. When superheating is at its maximum the total COP is 2.5, with minimal superheating the total COP is 3.2. (4) states this constraint.
Important parameters to consider are the operating temperatures and pressures. Many refrigerant options are available when selecting a chiller, the application, cooling temperature requirements, and refrigerant's cooling characteristics need to match. A vapor-compression chiller uses a refrigerant internally as its working fluid.
The refrigerant vapors are compressed to raise the pressure adequately for condensing by a heat sink. Usually, the heat of vaporization isothermally transfers heat from the refrigeration to the process yielding a lower temperature of the process fluid. In some processing schemes, the refrigerant is delivered directly to chillers and in other schemes chilled water or other medium is delivered to the process.The typical refrigeration cycle consists of two isothermal and two isenthalpic or adiabatic steps at isobaric conditions. Ethylene (often cascaded with propane), and Among some of the refrigerants used are:
The optimum will be affected by the weather conditions of ambient temperature and humidity that affect wet bulb temperature. The cost of refrigeration consists of fan motors, cooling tower pumps, and refrigerant compressors.There will be an optimum approach above the wet bulb temperature for supplying cooling water for refrigerant condensation and an optimum range, which is defined as the difference between the cooling water return and supply. In all cases, the maximization of the value of incremental recovery or yield less the additional cost of refrigeration will determine the optimum process temperatures. Often lower process temperatures will result in higher recovery, yield, or throughput and then the lowest refrigerant temperature (lowest refrigerant compressor suction pressure) will result in optimum operation. The main cost of condensing in either case is the horsepower required for circulating the air and cooling towers require the additional costs of pumping and treating the cooling water.In general, when adequate refrigeration is available, the highest refrigerant supply temperature that will satisfy the process needs will result in the least cost.
However, this creates an increase in the compression ratio for a given condensing temperature. For instance, cells with fans operating at high speeds should attain high water rates, cells at low speed take low water rates, and cells with fans that are off should receive minimum water rates.Lower suction pressures normally lead to colder refrigerant temperatures leading to more efficient chilling. When less cooling tower fan horsepower is required, fans can be stopped, slowed down, or the blade pitch varied, if these capabilities exist.The water flows to individual cells of the cooling tower should be adjusted to correspond with fan operation. Each 1☏ reduction in cooling tower supply temperature results in about a 1.5% improvement in efficiency.As the approach to wet bulb temperature decreases, the costs of pumping cooling water and compressing refrigerant decrease, whereas the cost of cooling tower fans increases. The cooling tower water supply temperature should not be held constant.
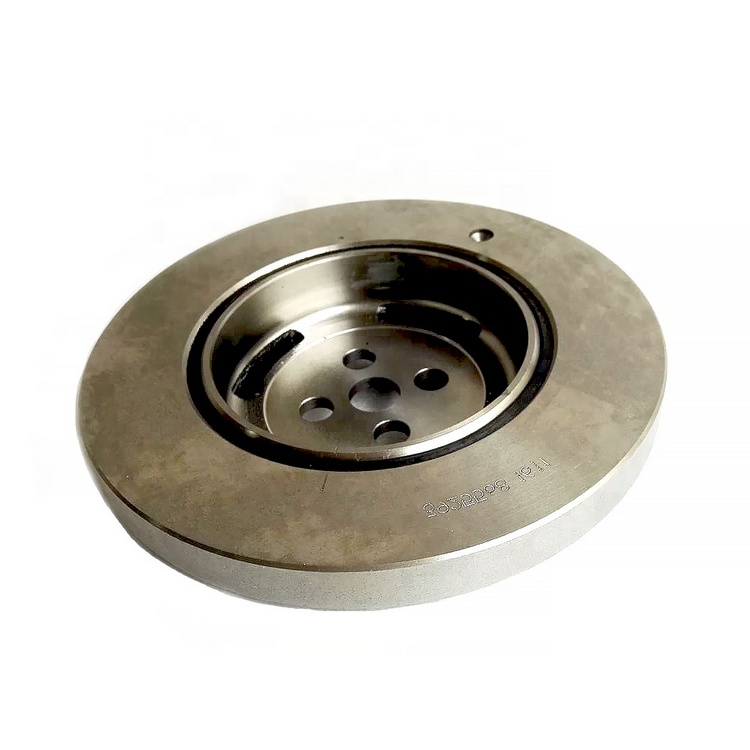
A disadvantage is the net pressure loss, which must be taken up by the export compressor. It is smaller and lighter than the refrigeration system. 9.9.3.4.2 Turbo-expanderThe turbo-expander serves the same purpose as a chiller, but has the benefit of being a dry system.
The control system shall monitor the common supply and return temperatures and provide a constant common supply water temperature, typically 40☏ (adjustable).If the chiller plant has cooling towers as a source of condenser heat rejection, then the condenser water supply temperature shall be controlled to optimize the plant energy use (check with chiller manufacturer for recommended set point values and allowable drop in temperature at times of low enthalpy outside air) by staging the cooling towers as necessary and cycling the cooling tower fans as required. The internal controls of the chiller shall operate each chiller to produce the required chilled water supply temperature. First the chillers respective chilled water primary pump may be energized and then the chillers respective condenser water pump (or condenser fan system) may be energized, then, several minutes later, after flow is proven at the pumps/fans/chiller, the respective chiller shall be enabled to operate and produce chilled water to the HVAC&R system. Eng., in Fundamentals of HVAC Control Systems, 2008 Chiller Plant, Pumps, and Boilers – Monitoring and ControlChiller and boiler plant control systems consist of controllers, sensors, relays, transducers, valves, and dampers that operate the plant and its equipment, as well as optimize it for energy conservation, efficiency, and functionality.On a demand for cooling, the chilled water system shall be enabled. An adsorbent guard bed is still required to remove heavy hydrocarbons but must be larger than it would normally be because it must also remove glycol carried over from the adsorber vessels.The reading text for this course was originally written by.
A high limit temperature sensor will operate the circulating pumps until the boiler internal temperature is at or below its set point. The boiler primary pump shall be operated at least 10 min before and after boiler is energized. Deadbands and time limits shall be set up such that the fans do not cycle unnecessarily.Some cooling tower plants have a bypass loop and internal sumps that allows bypassing of water around the towers in order to maintain minimum set points during cold and below freezing ambient conditions.On a call for heating, the plant control system shall start the boiler primary pump, and then the boiler shall be started–stopped.
The secondary loop, via its secondary distribution pumping system, takes water from the primary loop as needed for the hydronic systems it serves. Primary Secondary Pumping SystemThe primary loop (chillers and pumps) provides the “header” with a constant flow of chilled water. In addition, some boiler plant controllers monitor outside temperature, and provide higher hot water supply temperature set points to be available during extreme cold ambient conditions.Figure 9-10. If multiple boilers are used, a control routine that starts and stops them is used to maintain an adjustable set point temperature of water in the loop or storage tank while maintaining an appropriate return water temperature.
